Ross Double Planetary Mixer Makes High Quality Syntactic Foam Plugs for Thermoforming Applications
Wednesday, April 17, 2019
BACKGROUND:
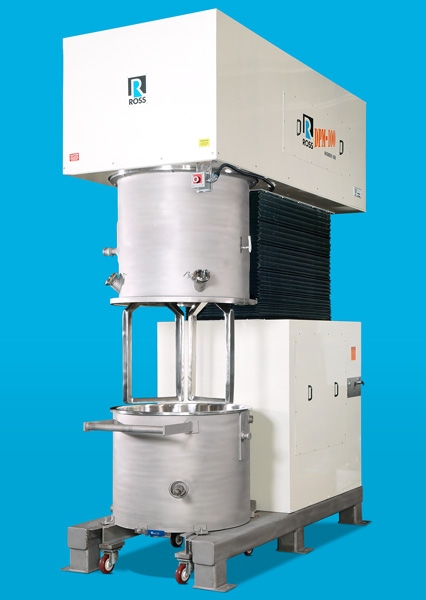
Ross Double Planetary Mixers, like this 25 gallon production unit, have been the mixers of choice for producing high quality, void-free Syntactic Foams.
Thermoforming is the process of forming thermoplastic sheet by the use of heat and pressure (or vacuum). Plastics such as polystyrene, polyethylene, ABS and polycarbonate are commonly formed by this method.
PROBLEM:
One method of Thermoforming utilizes a male plug to assist the vacuum or pressure in forming the plastic part. These plugs have traditionally been machined from blocks of aluminum which can be expensive. In addition, the aluminum plugs usually need to be temperature controlled - plugs that are too hot can result in plastic sticking to the plug; plugs that are too cold can promote “freezing” or premature hardening of the plastic resulting in an improperly formed plastic part.
SOLUTION:
Syntactic Foam plugs have been used very successfully as a substitute for aluminum plugs. Syntactic foams are microsphere filled resins such as epoxies or polyurethanes. They are characterized as having low densities and high compressive strengths, but more importantly for Thermoforming applications, they are thermally insulating materials, neither chilling or heating the plastic being formed. The end result is a material that is easily machined to any shape -and ultimately, a less costly Thermoforming plug.
PROCESSING:
Syntactic Foams require careful mixing techniques to insure their low density, high strength characteristics. In addition, the shapes that are cast must be completely void free. Any pores or voids in the finished plug would transfer that defect to the molded plastic part.
The Ross Vacuum Double Planetary Mixer is employed by companies worldwide for Syntactic Foam production. The gentle, yet thorough mixing action insures complete mixing of the hollow microspheres and resins while minimizing the number of fractured microspheres.
In a typical procedure, liquid components are first added to the mix can of the Double Planetary Mixer. The fragile microspheres are then charged to the resin while the stirrers of the Double Planetary mixer rotate and revolve. When the microspheres have been wetted, a vacuum of at least 29.5" Hg is drawn on the batch to remove air that can result in voids in the casting.
The finished material is usually pourable and can be cast by tilting the mix can or by opening a flush mounted ball valve in the bottom of the mix can. More viscous formulations can be discharged using a Ross Follower Plate Discharge System. The platen of the discharge system forces the product through a flush mounted ball valve in the bottom of the mix can.
The product is usually cast directly from the mix can into molds. These molds can form either net shape parts, or blocks from which finished parts are machined.
Ross Follower Plate Discharge Systems, like this elevated
configuration, can be used to discharge viscous Syntactics
from the mix can of a Double Planetary Mixer.
MIXER SPECIFICATIONS:
Some of the recommended features for Double Planetary Mixers used for Syntactic Foams include:
- Vacuum processing capability - allows the removal of air from the product, resulting in a stronger, void free casting.
- Variable speed control - enables the user to fine tune the charging sequence and the final mixing sequence.
- Jacketing of the mix can - lets the user control the temperature of the batch. Heating of the resin low ers viscosity, allowing higher solids loadings; cooling the batch can control the exotherm of roomtemperature curing resin systems, yielding longer pot life.
- Sight ports and charging ports - allow the operator to view the batch and to add in gredients without opening the mixer
- Thermocouple - flush mounted to the mix can wall can be used to monitor batch temperature and to give early warning of exotherms
- Flush mounted ball valve - in the bottom of the mix can facilitates the discharge of product with minimal dead space between stirrer and bottom of mix can
- Caster wheels - on the mix can promote easy movement of the mix can in and out of the mixing position. Other options that may be considered, depending on the specific application include:
- Dust shield - beneath the planetary gearbox reduces dusting in the upper gearbox area.
- Teflon scraper blades - to scrape the sides and bottom of the mix can are useful for ensuring batch homogeneity and promoting better thermal transfer from a jacketed mix can.
- Mechanical seals and gearbox caps - are important when using aggressive solvents, to prevent the breakdown of gearbox lubricants. Solvent resistant lubricants are also recommended for these applications
Important Note: Blade-to-bowl and blade-to-blade clearances on Double Planetary Mixers, for Syntactic Foam applications, should be liberal (1/8" for lab mixers and 1/4" - 3/8" for production units) to prevent excessive breakage of microspheres.