ROSS VersaMix with SLIM Produces Viscous Carboxy-Methylcellulose Gels for the Pharmaceutical Industry
Saturday, February 2, 2019
.jpg)
BACKGROUND
Carboxymethylcellulose (CMC) is a cellulose-derived water-soluble polymer, principally used as a water binder, thickening agent, suspending agent and emulsion stabilizer.
Applications for CMC are in the manufacture of detergents, soaps, food products, textiles, paper coatings, drilling muds, emulsion based paints, cosmetics and pharmaceuticals.
One important use of CMC is in the prevention of post-surgical adhesions, one of the major complications of surgery which can lead to bowel obstruction, abdominal and pelvic pain and infertility.
PROBLEM
Although many applications that require the use of CMC use low percentages (<2%), most medical gels require a loading of CMC that will result in extremely high viscosities (1 million+ cps). Often, CMC loadings of 4% or greater are required to give the final product its desired viscosity.
Conventional agitators (axial / radial flow impellers, sawtooth dispersers) are unable to create the fluid circulation necessary to properly disperse 4%+ powdered CMC dispersions. The consequence of insufficient agitation is the formation of non-dispersed lumps of CMC that may never be dispersed into the viscous bulk.
Once the bulk becomes highly viscous, it becomes extremely difficult to wet additional CMC into the bulk. Powder will tend to remain on the surface and not get drawn down into the bulk.
SOLUTION
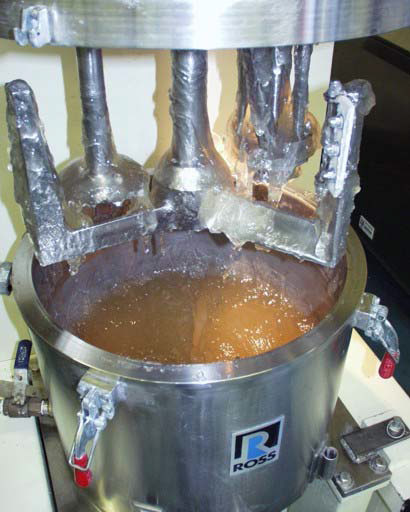
The Ross VersaMix, a versatile multi-agitator mixing system has the high-shear mixing capability and the flow generating capability to disperse and mix high percentage CMC dispersions.
The VersaMix consists of a three-wing anchor agitator, a sawtooth high speed disperser and a rotor/stator High Shear Mixer. The High Shear Mixer (HSM) can be combined with the Solid Liquid Injection Manifold (SLIM), a feature that takes advantage of the vacuum that normally occurs behind the rotor. This vacuum will provide the motive force to draw powdered ingredients down below the surface, directly into the high shear zone of the HSM.
By introducing the powder into the high shear zone, the CMC is instantly dispersed without the chance of agglomeration formation.
PROCEDURE
In order to produce high percentage CMC dispersions, the full amount of liquid (usually water) is added to the mixing vessel of the VersaMix.
All three agitators are turned on, the Anchor and Disperser to their mid-range speed, and the HSM with SLIM to its highest speed. The wand arrangement connected to the SLIM is placed in the powder container or bag, and the powder induction valve is opened.
The CMC powder is drawn into the wand and injected into the rotor / stator zone, where it disperses immediately. Seconds after the full amount of CMC has been dispersed, it hydrates and the viscosity quickly builds.
At this point, the HSM can be turned off, and the Anchor and Disperser turned to their highest speed.
If a clear, air-free CMC gel is required, vacuum can be drawn on the vessel to deaerate the bulk.